CHAPTER 1 GENERAL INFORMATION, EQUIPMENT DESCRIPTION AND THEORY OF OPERATION FOR FUEL DISTRIBUTION SYSTEM (FDS)GENERAL INFORMATIONCORROSION PREVENTION AND CONTROL (CPC)NOMENCLATURE CROSS-REFERENCE LISTSAFETY, CARE, AND HANDLINGCALIBRATION, REPAIR PARTS AND SPECIAL TOOLS, TMDE, AND SUPPORT EQUIPMENTFigure 1. Fuel Distribution System.Table 1. Fuel Distribution System Cart.Table 2. Power Cable and Switch Box.Figure 4. Filter Cartridge and Shell.Table 4. Flow Meter.Figure 6. Discharge Hose and Fuel Nozzle.Figure 7. Self-Priming Pump/Motor.Figure 8. Grounding Reels and Ground Clip.Figure 9. Cargo Container and Tires.Table 9. FDS Equipment Data.THEORY OF OPERATIONFDS Static Charge DissipationCHAPTER 2 OPERATOR INSTRUCTIONS FOR FUEL DISTRIBUTION SYSTEM (FDS)DESCRIPTION AND USE OF CONTROLS AND INDICATORSTable 2. Toggle Switch.Table 3. Flow Meter.Figure 4. Differential Pressure Gauge.Fuel Nozzle Lever.Figure 6. Self-Priming Pump Intake Valve.OPERATION UNDER USUAL CONDITIONSFilter Shell.SCS Unfolded.Three Walls Standing.Figure 6. Pump Intake Female Valve and Suction Hose.Figure 7. Suction Hose Secured.Figure 9. Dispensing Nozzle OFF/Closed.Toggle Switch OFF.Figure 12. Hose Reel and Brake.Figure 13. Fuel Nozzle Housing.Filter Vent Valve.Figure 17. Gauge Needle in Normal Zone.Toggle Switch OFF.Figure 21. Fuel Nozzle Housing.Figure 22. Drained Pan Beneath Pump Inlet.Drain Discharge HoseDrain PumpFilter Vent Valve.Priming Port.Drain Cap Removed.Figure 33. Filter Drain Valve Opened.Drain Cap Replaced.Toggle Switch OFF.Figure 38. Power Plug Removed.Figure 40. Hose Reel Brake Wheel Tightened.Figure 41. Suction Hose Disconnected.Figure 43. Dust Plugs and Caps.Wall Supports.16. Ensure SCS is dry and clear of debris.DECALS AND DATA PLATESFigure 3. Pump Liquid Temperature Warning Tag.Figure 6. Hose Reel and Pump Motor Data Plates.Filter Decal.OPERATING UNDER UNUSUAL CONDITIONSOPERATION IN STRONG WINDS AND SANDY OR DUSTY CONDITIONSOPERATOR INSTRUCTIONS EMERGENCYFUEL LEAK DURING OPERATIONCHAPTER 3 TROUBLESHOOTING PROCEDURES FOR FUEL DISTRIBUTION SYSTEM (FDS) OPERATOR\CREWOPERATOR\CREW TROUBLESHOOTING INDEXOPERATOR\CREW TROUBLESHOOTING PROCEDURESFlow meter is not showing fuel amounts correctly or is not working.FDS cam-locking ittings include the pump inlet assembly, priming port, and ilter drain.CHAPTER 4 TROUBLESHOOTING PROCEDURES FOR FUEL DISTRIBUTION SYSTEM (FDS) MAINTAINERMAINTAINER TROUBLESHOOTING INDEXMAINTAINER TROUBLESHOOTING PROCEDURESReplace toggle switch, if it is not functional (WP 0040).Tighten fasteners retaining langes together (WP 0026, WP 0036).CHAPTER 5 MAINTENANCE INSTRUCTIONS FOR FUEL DISTRIBUTION SYSTEM (FDS)OPERATOR\CREW PREVENTIVE MAINTENANCE CHECKS AND SERVICES (PMCS) INTRODUCTIONOPERATOR\CREW PREVENTIVE MAINTENANCE CHECKS AND SERVICES (PMCS)OPERATOR\CREW PREVENTIVE MAINTENANCE CHECKS AND SERVICES (PMCS)OPERATOR\CREW PREVENTIVE MAINTENANCE CHECKS AND SERVICES (PMCS)OPERATOR\CREW PREVENTIVE MAINTENANCE CHECKS AND SERVICES (PMCS)OPERATOR\CREW PREVENTIVE MAINTENANCE CHECKS AND SERVICES (PMCS)OPERATOR\CREW PREVENTIVE MAINTENANCE CHECKS AND SERVICES (PMCS)Table 3. Operator/Crew PMCS For FDS -- After.Table 3. Operator/Crew PMCS For FDS -- After.Table 3. Operator/Crew PMCS For FDS -- After.REPLACE FILTER CARTRIDGERemove Filter CartridgeFigure 2. Filter Cartridge and Shell.Filter Head.New Filter Cartridge.Knobs and Clamps.Filter Vent Valve.CLEANINGPAINTINGPREPARATION FOR STORAGE OR SHIPMENTCHAPTER 6 - MAINTENANCE INSTRUCTIONS FOR FUEL DISTRIBUTION SYSTEM (FDS)SERVICE UPON RECEIPTMAINTAINER PREVENTIVE MAINTENANCE CHECKS AND SERVICES (PMCS) INTRODUCTIONMAINTAINER PREVENTIVE MAINTENANCE CHECKS AND SERVICES (PMCS)Table 2. Maintainer PMCS For FDS -- After.MANDATORY REPLACEMENT PARTSSERVICE FUEL DISTRIBUTION SYSTEMGrease Fittings.TIRE INFLATION SERVICEREPLACE POWER PLUGPlug Wires.Plug Assembled.Figure 5. FDS Electrical Wiring Diagram.REPLACE POWER CABLESGland Nut.Switch Cover.Section 1 - Cable (Power Plug to Toggle Switch) InstallationFigure 6. Cable Inserted Into Gland Nuts.Figure 8. Corrosion Preventive Compound on Cover Flange.Figure 10. Attached Switch Cover.Figure 12. Switch Enclosure and Gland Nut.Figure 14. Remove Wire Nuts and Cable.Figure 16. Pump Motor Electrical Enclosure.Figure 18. Insertion of Cable through Gland into Housing.Figure 19. Pump Motor Electrical Enclosure.Figure 23. Toggle Switch Wiring Diagram.Figure 24. Corrosion Preventive Compound.Attach Switch Cover.Figure 28. FDS Electrical Wiring Diagram.REPLACE FUEL NOZZLE HOUSING LOCKING PLATEFigure 2. Fasteners and Plate Removed.Locking Plate Closed.Intiial SetupCable and Gland Nut.Figure 2. Unscrewed Cable Gland.Figure 3. Pump Motor Enclosure.Figure 4 PumpFigure 5. Flange Union and Gasket.Figure 6. Pump Removed from FDS.Pump Disassembly.Repair PumpPump Assembly.Check Valve.Figure 11. Flange Union Gasket.Fasteners.Figure 13. Flange Bolt Tightening Sequence.Pump Drain Tube.Figure 15. Cable Gland and Gland Nut.Figure 17. Pump Motor Electrical Enclosure.Figure 18. Cable Gland and Gland Nut.Figure 20. FDS Electrical Wiring Diagram.REPAIR PUMPPump Inlet.Clean and Inspect Pump InletPriming Port.REPAIR PUMP DRAIN ASSEMBLYRemove Pump DrainPump Drain Parts.Repair Pump DrainFigure 3. Drain Tube Prepared for Installation.Perform operational test IAW WP 0005.REPLACE DIFFERENTIAL PRESSURE GAUGERemove Differential Pressure GaugeFigure 2. Differential Pressure Gauge Removed.Figure 4. Tapered Threads on Compression Fittings.Figure 6. Fittings Added to New Gauge.Figure 7 Compression Nuts.Perform operational test, check for leaksREPAIR FILTER DRAIN ASSEMBLYRemove Filter Drain AssemblyFigure 2. Filter Drain Assembly Parts.Repair Filter Drain AssemblyFigure 4 DrainREPLACE GROUNDING REELGrounding Reel Feet.Measure resistance between the ground clipsREPAIR GROUNDING REELFigure 2. Ground Wire Loop Attached to Ground Clip.REPLACE HOSE REEL ASSEMBLYHose Reel.Figure 2. Hose Reel Nuts and Bolts.Figure 5. Hose/Riser Assembly Removed from Hose Reel Assembly.O-ring between hose/riser assembly and hose reelFigure 6. Hose Assembly Remove from Riser.Install Hose AssemblyFigure 8. Hose/Riser Assembly Assembled onto Hose Reel Assembly.Install Hose Reel AssemblyHose Reel Assembly.Hose reel assembly may need to be pivotedFigure 10. Hose Reel Assembly Rewind.REPLACE FUEL NOZZLELocking Pin.Figure 2. Safety Ring Removed from Groove.Install Fuel NozzleREPLACE SWIVEL JOINTRemove Cargo ContainerCargo Container.Brake Assembly.Figure 5. Swivel Joint and Pipe Assembly.Figure 6. Swivel Joint Turned via Flats.INSTALL SWIVEL JOINT AND CARGO CONTAINERFigure 9. Hose Reel Threaded Hub.Figure 11. Pipe Assembly Attached to Flow Meter Flange.Figure 12. Swivel Joint and Reel Threaded Hub.Figure 13. Brake Pad, Spring and Wheel.REPLACE FLOW METERHairpin Cotter Pin.Latch Handle.Cargo Container.Figure 5. Lowered Pipe Assembly.Install Flow MeterFigure 8. Raised Pipe Assembly.Attached Flow Meter.REPAIR CARGO CONTAINERLatch Handle.Remove Cargo Container LidRepair Cargo ContainerFigure 7. Lid and Hinge Attachment to Cargo Container Box.REPLACE CARGO CONTAINER LATCHCargo container has to be removed to replace the keeper, and if latch is replaced, all of the latch is replaced.Figure 2 LatchKeeper Removed.Install LatchInstall hairpin cotter pin on latch.REPLACE TIRETire Installation.REPAIR TOGGLE SWITCH ASSEMBLYToggle Switch.Switch and Cover.Repair Toggle SwitchFigure 4. Switch Cover Assembly.Figure 5. Black Wires Attached to Toggle Switch.Figure 7. Corrosion Preventive Compound Applied.Figure 9. FDS Electrical Wiring Diagram.MANUFACTURING POWER CABLE PROCEDURESSection 2 Cable.MANUFACTURING DISCHARGE HOSE PROCEDURESFigure 2. Preformed Band on Hose.Figure 4. Pumping Ratchet Wrench.Figure 5. Band Clamp Marked with Lines.Figure 6 Buckle Secured.14. Repeat task for remaining band or remaining hose-end if needed.MANUFACTURING PUMP DRAIN TUBE PROCEDURESCHAPTER 7 PARTS INFORMATION FOR FUEL DISTRIBUTION SYSTEM (FDS)REPAIR PARTS AND SPECIAL TOOLS LIST (RPSTL) INTRODUCTIONTable 2. Source Code Explanation.Cannibalization or controlled exchange, when authorized, may be used as a source of supplyApplication/ExplanationEXPLANATION OF CROSS-REFERENCE INDEXES WORK PACKAGES FORMAT AND COLUMNSABBREVIATIONSFigure 1. Fuel Distribution System.Figure 2. Centrifugal Pump Unit.Figure 3. Pump Drain Assembly.Figure 4. Differential Pressure Gauge.Fluid Filter Element.Filter Drain Assembly.GROUNDING REELHose Reel Assembly.Discharge Hose.Figure 10. Fuel and Oil Servicing Nozzle.Swivel Joint.FLOW RATE INDICATING METERTOOL SHIPPING AND STORAGE CONTAINERFigure 14. Cargo Container Latch.Figure 15 - TireTOGGLE SWITCH ASSEMBLYFIELD MAINTENANCE BULK ITEMS LISTNATIONAL STOCK NUMBER INDEXPART NUMBER INDEXPART NUMBERCHAPTER 8 SUPPORTING INFORMATION FOR FUEL DISTRIBUTION SYSTEM (FDS)REFERENCESMAINTENANCE ALLOCATION CHART (MAC) INTRODUCTIONchemical luids, or gasesExplanation Of Columns In The MACExplanation Of Columns In The Tools And Test Equipment RequirementsMAINTENANCE ALLOCATION CHART (MAC)Tools and Test Equipment for FDS.Service consists of checking tire pressureCOMPONENTS OF END ITEM (COEI) AND BASIC ISSUE ITEMS (BII) LISTSComponents of End Item List.ADDITIONAL AUTHORIZATION LISTEXPENDABLE AND DURABLE ITEMS LISTEXPENDABLE AND DURABLE ITEMS LISTTOOL IDENTIFICATION LISTTOOL IDENTIFICATION LISTMANDATORY REPLACEMENT PARTS LIST
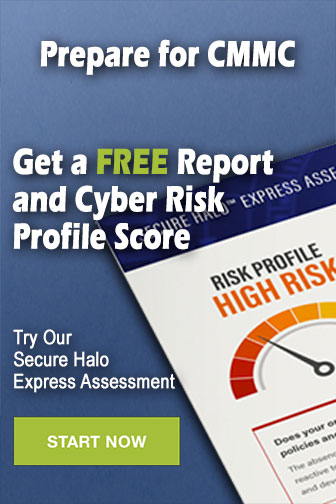